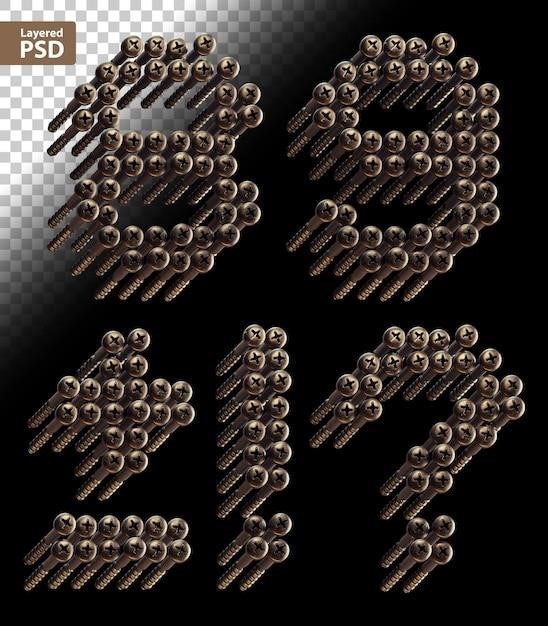
Flange Bolt Tightening Sequence⁚ A Comprehensive Guide
This guide details flange bolt tightening procedures, emphasizing the crucial role of proper sequence for leak-free joints. Various methods, including star patterns and sequences for different bolt numbers (4-bolt to 24-bolt and larger), are explained. Factors influencing torque and common mistakes are also addressed.
Importance of Proper Sequence
The sequence in which flange bolts are tightened significantly impacts the overall joint integrity and sealing effectiveness. A haphazard approach can result in uneven clamping force distribution, leading to gasket deformation or failure. This uneven pressure may cause leaks, especially in high-pressure applications. Following a prescribed sequence, such as the common star pattern, ensures that the gasket is compressed uniformly across its entire surface. This uniform compression helps to create a consistent seal, preventing leakage and maintaining the structural integrity of the flanged connection. Ignoring proper sequence can lead to premature gasket wear, bolt damage, and ultimately, system failure. The correct method minimizes stress concentrations on individual bolts and the gasket, ensuring a longer service life for the entire assembly. In critical applications, adhering to the specified sequence is non-negotiable for safety and operational reliability.
Star Pattern Tightening⁚ A Common Method
The star pattern is a widely used and effective method for tightening flange bolts. It involves tightening bolts in a sequence that progresses from the center outward, resembling a star. This method ensures even gasket compression and minimizes stress concentrations. Starting at a central bolt, the next bolt tightened is diametrically opposite. Subsequent bolts are tightened in a progressive, alternating pattern, moving outwards towards the flange periphery. This approach helps to distribute the clamping force evenly across the gasket surface. The star pattern is particularly beneficial for larger flanges with numerous bolts. It prevents uneven tightening and the potential for gasket blowouts or leaks. While simple in concept, consistent and careful execution is key to achieving uniform stress distribution. Variations on the star pattern exist, adapting the sequence to specific flange geometries and bolt configurations. Properly executed, this method optimizes seal integrity and extends the life of the bolted joint.
Tightening Sequences for Different Bolt Numbers
The optimal tightening sequence varies considerably depending on the number of bolts in the flange. For simple 4-bolt flanges, a criss-cross pattern is often sufficient. This involves tightening diagonally opposite bolts sequentially until the desired torque is reached. As the bolt count increases (8, 12, 16, and beyond), more sophisticated patterns are necessary to ensure even stress distribution. The star pattern, mentioned previously, is highly effective for larger flanges. For 12-bolt and 16-bolt flanges, a modified star pattern or a progressive circular pattern might be employed. These patterns maintain the principle of gradually increasing the clamping force across the entire gasket surface. For extremely large flanges (e.g., those with 20, 24, or more bolts), the tightening process can be broken down into stages, often employing a grouping technique where sets of adjacent bolts are tightened as units. These techniques require careful planning and precise execution to prevent uneven stress and potential gasket damage. Detailed diagrams and instructions are usually included in flange assembly specifications or manufacturer guidelines.
4-Bolt and 8-Bolt Flange Tightening
For 4-bolt flanges, a simple criss-cross pattern is generally sufficient to achieve uniform gasket compression. Begin by tightening one bolt, then move diagonally opposite to tighten the second. Repeat this process for the remaining bolts, ensuring each bolt reaches the specified torque. This ensures even load distribution and prevents gasket distortion or leakage. With 8-bolt flanges, a more systematic approach is usually recommended. One common method is a modified criss-cross, where you progress through the bolts in a pattern that ensures no adjacent bolts are tightened consecutively. This minimizes the risk of uneven stress. Another option is a sequential pattern, moving around the flange in a circular manner. Irrespective of the selected pattern, the key is to maintain a consistent incremental tightening approach. Avoid over-tightening any single bolt. Always refer to the manufacturer’s specifications for the recommended torque and tightening sequence for the specific flange and gasket material. Using a torque wrench calibrated for accuracy is essential to prevent damage to the bolts or flange. Proper lubrication of the bolt threads and contacting surfaces can also improve the uniformity of the tightening process and reduce friction.
12-Bolt and 16-Bolt Flange Tightening
Tightening 12-bolt and 16-bolt flanges requires a more precise approach than smaller flange configurations. The star pattern, starting from the center and progressing outwards, is frequently employed for these larger bolt counts. This method helps distribute clamping force evenly across the gasket. For 12-bolt flanges, begin by tightening bolts in the center, then work your way outwards in a star pattern, ensuring that no two adjacent bolts are tightened consecutively. This methodical approach prevents uneven stress and potential gasket damage. The 16-bolt flange tightening sequence follows a similar principle to the 12-bolt sequence. The star pattern is still effective in ensuring even distribution of torque. However, due to the larger number of bolts, more passes may be required to achieve uniform tightening. Remember to consult the flange manufacturer’s specifications for the recommended torque values and the specific sequence to use. Utilizing a calibrated torque wrench is paramount; it prevents over-tightening and bolt damage. Consistent, incremental tightening, along with proper lubrication, contributes to a secure and leak-free seal. Multiple passes are usually recommended, increasing the torque gradually in each pass to guarantee uniform clamping force across the gasket.
20-Bolt and 24-Bolt Flange Tightening
Securing 20-bolt and 24-bolt flanges demands a systematic approach to ensure uniform gasket compression and prevent leaks. While the star pattern remains a viable option, its application becomes more complex with the increased number of bolts. A modified approach, sometimes involving dividing the bolts into groups, might be more practical. For instance, you could divide the 20 bolts into five groups of four and tighten them sequentially, using the star pattern within each group. This ensures a more even distribution of clamping force. With 24-bolt flanges, a similar approach could be employed by dividing them into six groups of four. Again, a star pattern is used within each group. This phased tightening allows for better control and minimizes the risk of uneven stress. Remember, consistent incremental tightening, rather than applying full torque immediately, is crucial. Multiple passes are usually necessary to achieve uniform bolt load. Always refer to manufacturer specifications for precise torque values and recommended sequences. Employing a calibrated torque wrench is crucial to avoid over-tightening and potential bolt damage. Proper lubrication of bolt threads and contact surfaces is essential to reduce friction and ensure accurate torque application. Careful attention to detail during this process is vital for the long-term integrity of the flange connection.
Larger Flange Bolt Grouping Techniques
For flanges exceeding 24 bolts, the complexity of achieving uniform tightening increases significantly. Simple star patterns become unwieldy and impractical. Instead, experienced technicians often utilize grouping techniques. This involves dividing the bolts into smaller, more manageable subsets. These subsets can then be tightened using modified star patterns or other sequential methods. The key is to ensure that the bolts within each group are tightened evenly before moving to the next group. One common strategy is to group adjacent bolts, treating each group as a single unit in a larger pattern. For example, a 48-bolt flange could be treated as twelve groups of four. A modified 12-bolt tightening sequence can then be implemented. Another approach involves dividing the flange into quadrants or sectors, tightening the bolts within each sector before proceeding to the next. The specific grouping strategy depends on flange geometry and the available tools. Regardless of the method, the principle remains consistent⁚ incremental tightening in a controlled manner is crucial to achieve uniform bolt load and prevent gasket damage or flange distortion. Accurate torque application, using calibrated tools, is essential throughout the entire process. Consult relevant standards and manufacturer specifications for the most effective approach for your specific flange design.
Factors Affecting Tightening Torque
Several factors significantly influence the torque required for proper flange bolt tightening. Bolt material properties, including tensile strength and yield point, directly impact the force needed to achieve a desired clamping load. The bolt diameter and thread pitch also play crucial roles; larger diameter bolts generally require higher torque. Gasket type and condition are critical. Different gasket materials (e.g., metallic, non-metallic) exhibit varying compression characteristics, demanding adjusted torque values. A compressed gasket’s condition, whether new or reused, affects its sealing ability and thus the required torque. Lubrication of the bolt threads and contact surfaces reduces friction, impacting the relationship between applied torque and clamping force; Well-lubricated bolts achieve greater clamping force with less torque. Environmental conditions, such as temperature, also affect the torque-clamping force relationship. Elevated temperatures can reduce bolt strength and alter gasket behavior. Finally, the accuracy of the torque wrench and the operator’s technique are essential for consistent and reliable tightening. Inconsistent tightening can lead to uneven stress distribution, compromised gasket sealing, and potential flange leakage or failure. Therefore, using calibrated tools and adhering to standardized procedures are paramount for achieving proper tightening.
Hot Torquing and Elevated Temperatures
Hot torquing is a specialized flange bolting procedure employed when operating temperatures significantly impact gasket performance and joint integrity. Unlike standard tightening at ambient temperatures, hot torquing involves tightening bolts while the flange assembly is at its operating temperature. This method compensates for gasket relaxation or creep that may occur at elevated temperatures. Gasket materials can lose their clamping force as temperatures increase, leading to potential leaks if tightened only at ambient temperatures. Hot torquing ensures sufficient clamping force is maintained even when the system reaches its operational temperature. The process typically involves heating the flange assembly to the desired operating temperature before tightening. Specific temperature ranges and procedures vary depending on the materials used and the application’s requirements. Precise temperature monitoring and control are critical during hot torquing to prevent damage to the gasket or the flange itself. The selection of appropriate bolt materials that can withstand elevated temperatures without significant strength reduction is also crucial. Special considerations may be needed for bolt materials and lubricants at high temperatures. Improper hot torquing can lead to joint failure, so adhering to established guidelines and using appropriate equipment is crucial for success.
Avoiding Common Mistakes in Tightening
Improper flange bolt tightening is a frequent source of leaks and equipment failure. One major error is neglecting the correct tightening sequence. Random tightening creates uneven stress distribution, leading to gasket deformation and potential leaks. Using the wrong torque value is another critical mistake; excessive torque can damage bolts or the flange itself, while insufficient torque results in inadequate sealing. Employing a calibrated torque wrench is essential for consistent and accurate tightening. Reusing old gaskets can also compromise the seal’s integrity, leading to leaks. Gaskets are designed for single use, and reusing them may result in uneven compression and reduced sealing effectiveness. Ignoring the importance of lubricant on bolt threads and under the bolt head is a common oversight. Lubrication reduces friction, contributing to more uniform bolt loading and minimizing the risk of galling. Failure to address flange misalignment before bolting is another significant error. Misalignment places uneven stress on the gasket, increasing the likelihood of leakage and premature failure. Finally, using improper gasket materials for the specific application and operating conditions can lead to sealing problems. Selecting the correct gasket material based on temperature, pressure, and fluid compatibility is crucial for a reliable seal.
Resources and Further Reading
For comprehensive guidance on flange bolt tightening, several valuable resources are available. ASME standards, such as ASME B16.5 and ASME B16.47, offer detailed specifications for pipe flanges and their associated bolting practices. These standards provide valuable insights into appropriate bolt materials, torque values, and tightening sequences for various flange types and sizes. Furthermore, manufacturer’s guidelines for specific equipment and components should always be consulted. These often contain detailed instructions for bolting procedures tailored to the particular design and operating conditions. Numerous online resources, including engineering blogs and technical articles, offer additional information on best practices and troubleshooting techniques. These resources often provide practical advice, case studies, and visual aids to supplement formal standards. Industry-specific publications and handbooks also provide valuable information relevant to particular applications. For example, publications focused on chemical processing, power generation, or oil and gas industries often contain specialized guidance on flange bolt tightening in those contexts. Finally, attending industry-relevant training courses or workshops can enhance practical understanding and skills in proper bolting techniques. Hands-on experience and expert guidance can be invaluable in mastering this critical aspect of industrial maintenance.